Digital Insights #55
How Covid is reshaping OEMs Part 1 of 3
Harinderpal Hanspal
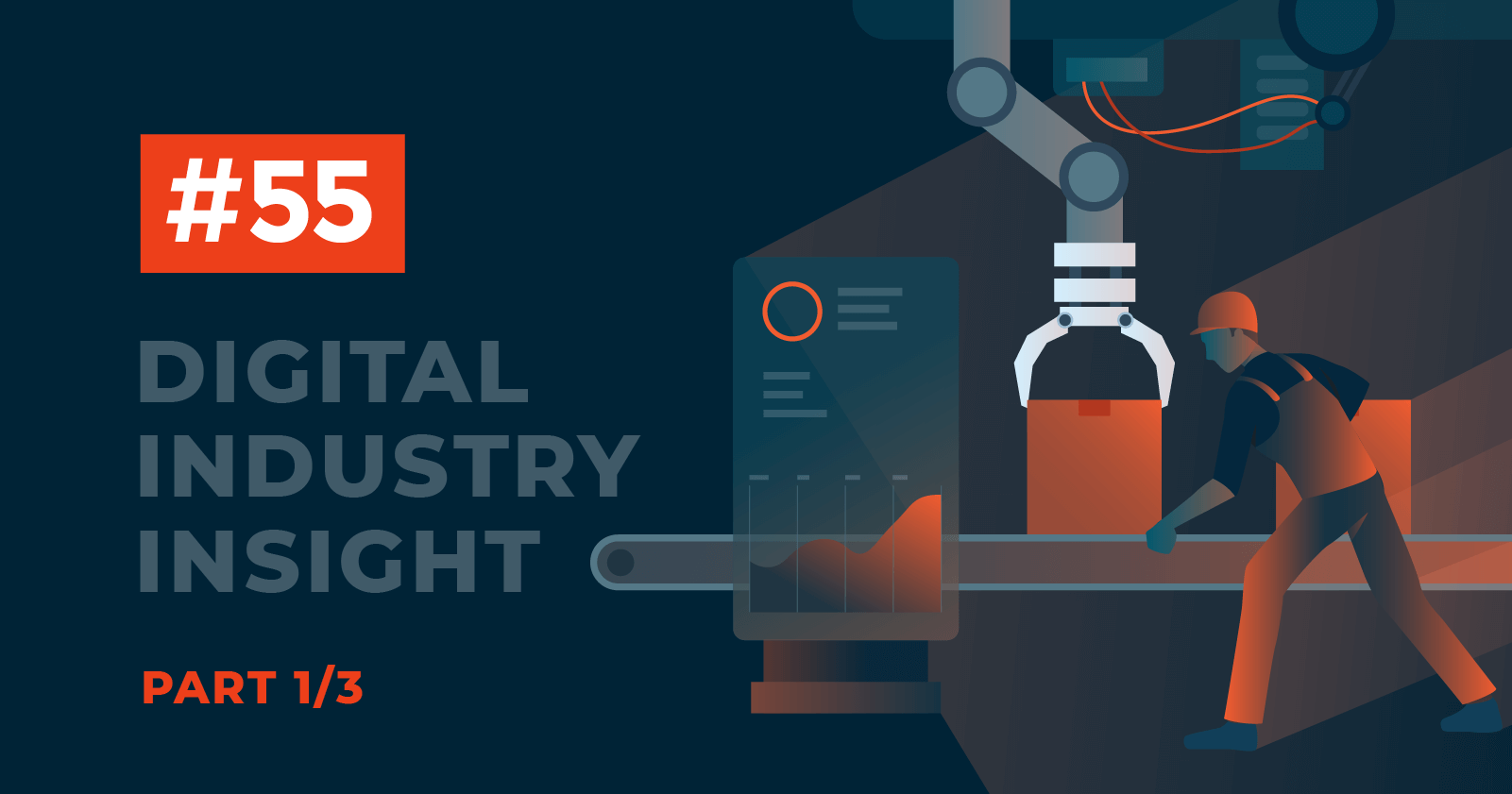
The Impact and Lessons of Covid on OEMs
This article is the first of a three-part series in which we will:
- Look at the impact & lessons of Covid on Original Equipment Manufacturers (OEM)
- Examine some of the critical enablers of a post-Covid OEM world
- Discuss what future versions of OEMs, the so-called OEM X.0 will look like
Covid's widespread impact not only amplified the supply chain challenges but also highlighted problems across an OEM's entire business operations due to shelter-in-place orders and social distancing guidelines:
- Designing & Building Products
Closure of laboratories, workshops, maker spaces, and factories halted researchers', engineers', and production managers' ability to work as they needed physical access to equipment and tools to perform their jobs. Manufacturers whose product demand increased could not keep up with demand due to reduced production capacity and supply chain disruptions. - Finding & Keeping Customers
Social distancing and customers' hesitancy in allowing visitors into their facilities made it difficult for sales to meet with customers and for field technicians to install and service equipment. When they allowed visitors, it was under strict safety policies that created scheduling challenges due to limited capacity. - Managing Ecosystem
International travel bans, delays in cross-border traffic, and lack of air or ocean freight capacity created shortages of raw materials, components, finished products, and spare parts. With suppliers shutting down, there was no visibility for OEMs into the availability of goods, forcing them to look for alternative suppliers. - Accessing Talent & Skills
Unemployment in manufacturing spiked to historically high levels as OEMs shut down their businesses for quarantine. Essential manufacturing businesses that remained open had to address employee concerns around safety and employee well-being, many of whom the pandemic impacted materially. - Controlling Revenue & Costs
Eight out of ten manufacturers expected financial losses from Covid's abrupt and massive disruptions in a survey by the National Association of Manufacturers. Some manufacturers – paper products, food & beverage, computers, and electronics products – experienced a slight to no drop in revenues. Other manufacturers – motor vehicles and fabricated metal products – saw a significant drop. For OEMs that continued to operate, supply chain disruptions and Covid-related health and safety changes led to increased costs.
As guidelines for opening manufacturing plants safely came out, OEMs repurposed their production lines to target needed products such as respirators, respirator parts, medical PPE, and hand sanitizers. Pivoting, where companies shift their business models to entirely new product lines, go-to-market channels, suppliers, or customer segments, is a common term in the tech community. With Covid, it became a verb in manufacturing too. OEMs that successfully pivoted identified three key areas that enabled them to pivot:
- Rapid Decision Making and Organizational Flexibility
Pivoting the entire business, from production lines, sales, and service to shipping and logistics, needed quick decision making and organization flexibility for actions such as setting up work-from-home capabilities, redesigning office and manufacturing spaces, and expanding sourcing partners. - Employee Skills and Know-How
With reduced capacity and staffing levels, employees needed to wear many hats, requiring diverse skill sets. - Technological Ability, Capacity Digital Technologies
Manufacturing firms with a high digitalization level were more technically adaptable than manufacturers with lower digital adoption in pivoting.
In recent years, the manufacturing industry has seen an increase in the number and frequency of supply chain disruptions due to trade wars, epidemics, and material shortages. In its 2006 Global Risks Report, the World Economic Forum identified infectious diseases as a significant risk. More recently, the reports have identified environmental issues - extreme weather, natural disasters, and climate action failure - as the highest risks, both in terms of the event's likelihood and its global business impact. To add resiliency and prepare for future disruptions, OEMs across industries are looking to reshore and localize production, change hiring and training practices, and invest in digital technologies. Post-Covid, pivoting will become a common term for Original Equipment Manufacturers.
Stay tuned to next week's sequel as Hans will be
examining critical enablers of a post-pandemic OEM world.
If you would like to hear more from Hans, listen to
Podcast #131 The Open Manufacturer:
Harinderpal (Hans) Hanspal is the Founder and Principal at Thing Company, where he advises companies on product, customer, and revenue strategies for "Everything-As-A-Service" (XaaS) business models. He is a technology industry veteran and startup entrepreneur who has helped create and grow several global technology-enabled businesses in industrial, technology, and telecom industries, including a successful startup exit as a founder. In his spare time, he leads Seattle's 4200+ member IoT Hub Meetup group.
Momenta encompasses leading Strategic Advisory, Talent, and Ventures practices with over 200 IoT leadership placements, 125 industry clients and 40+ young IoT disruptors in our portfolio.
Schedule a free consultation to learn more about our Digital Industry practice.